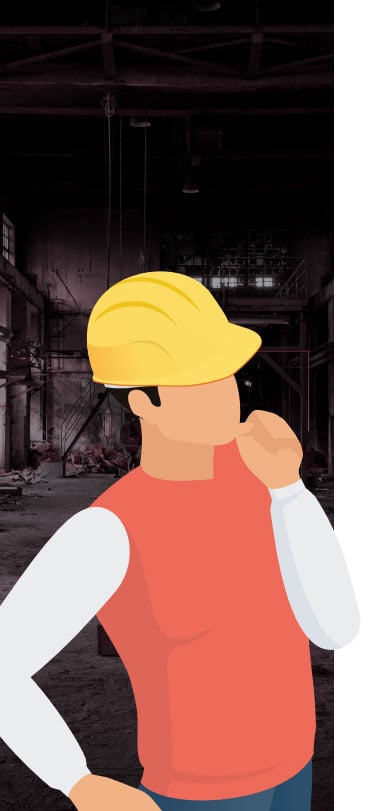
Scary Construction Project Management Mistakes
Construction is one of the riskiest businesses, with high rates of business failure and bankruptcy, razor-thin margins and subcontractors trying to control the hundreds of project elements that can cause delays or threaten profitability. Still, the global construction industry is headed for major growth over the next decade, with at least one major report anticipating major construction growth and investment in India, China and the United States. To take advantage of that growth, subcontractors need to get their operations in order when it comes to effective project management that an guarantee profitability while mitigating risk. To point you in the right direction, we’ve highlighted the seven scary construction project management mistakes that are rampant in the industry today and offered our best solutions for how to avoid committing them at your construction or subcontracting firm.
In this eBook you’ll learn:
- Inefficient labor productivity
- Inaccurate job costing and project estimates
- Poor project visibility
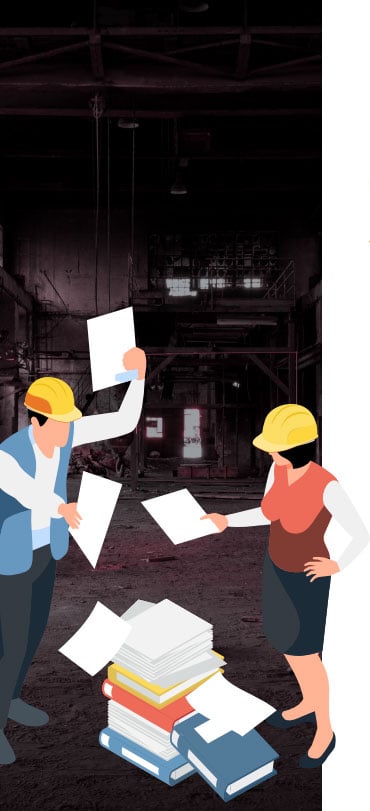
Failure to Adequately Control Documents
Construction documents are the reference material at the core of any project. Construction projects generate hundreds or thousands of pages of documentation, and without the ability to organize that documentation and send it to the right place to make it accessible for the right people, construction project managers and subcontracting organizations can find themselves in jeopardy.
Consider the following: a report by the Construction Institute, titled A Guide to Construction Rework Reduction, indicates that up to 20% of the cost for a typical construction project is derived from rework. The same study investigated the root cause of rework on the job site and came to some alarming conclusions about the nature of construction rework:
- 3% of construction rework is caused by inferior construction coordination
Work was done in an improper order, so needs to be re-done to be finished correctly; often caused by a scheduling error. - 18% of construction rework is caused by poor quality and safety training
A rework is needed to meet certain quality or safety standards that the worker was unaware of when the work was initially completed. - 24% of construction rework is connected to supply chain management problems
Time-sensitive work needed to be completed to avoid a rework, but the materials shipped too late and the work had to be re-started when the materials arrived. - 55% of construction rework is caused by inaccurate documentation
Someone did the work without referencing the correct version documents, plans, or change order and rework is necessary to meet the required specifications.
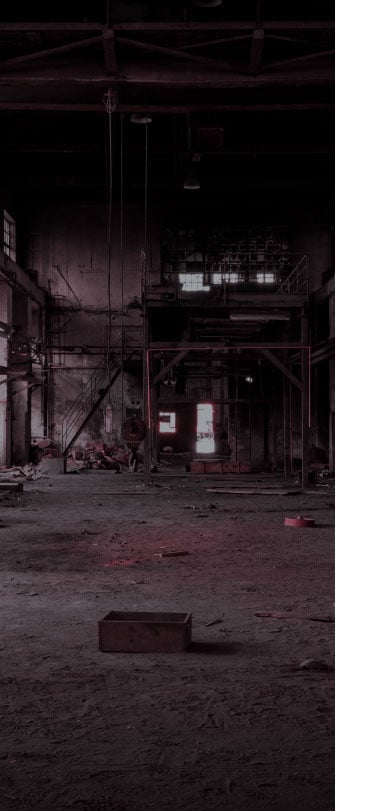
Subcontractors deal with reams of paperwork for each new construction project, including the project contract, drawings, daily progress and field reports, submittals, change order requests, purchase orders, time cards, safety guidelines, meeting minutes, inspection checklists and more. On the job site, workers need instant access to the most current and up-to-date drawings and documents to ensure that tasks are completed to the relevant specifications.
To satisfy their need for effective document sharing and control, subcontractors need to:
- Get away from storing project information in personal e-mail accounts, Google drives and Dropbox folders — subcontractors need to establish a central repository that acts as a single source of truth for project documentation. This ensures that workers in the back office and on the job site have access to the most updated project documents for editing, sharing and referencing as needed.
- Organize files in a logical and searchable format that makes it easy for staff in the back office and on the job site to quickly find the information they need.
- Track revisions to documents in the central repository and keep records of how documents change over time, creating a strong audit trail throughout the documentation system.
Subcontracting organizations are increasingly adopting construction project management software solutions like eSUB to facilitate better documentation practices that reduce or eliminate costly rework.
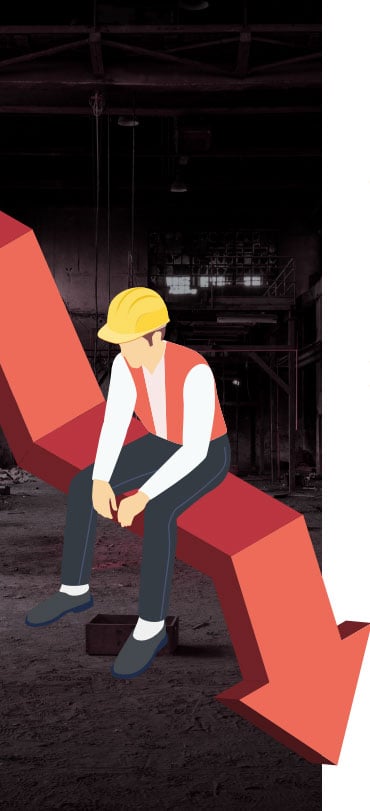
Insufficient Labor Productivity
One of the major challenges faced int he construction industry in 2020 is an ongoing shortage of labor. A 2020 report from the Associated General Contractors of America reveals that the construction industry has lost 975,000 jobs in April from a deteriorating demand for construction due to the COVID-19 pandemic. Also, from a survey of over 800 construction firms, 67% of firms have reported to canceling or delaying projects since the start of the outbreak in early March. Further, 80% of subcontractors report that they are having difficulty filling craft positions, the most important labor-performing roles on the job site.
Dealing with a shortage of qualified talent for hire has become part of reality for subcontractors, making it even more important for subcontractors to monitor and optimize the productivity of their existing labor force. Subcontractors often deliver project estimates or schedule project timelines that depend on certain levels of worker productivity — but without the right systems in place to monitor and increase productivity, these estimates can amount to guesswork or even wishful thinking.
Data from the Independent Project Analysis Group also tells us that 35% of all construction projects will have a major change somewhere during the project, and often the project owner still wants the entire job completed by the promised date. Unexpected changes to projects create inefficiencies that may negatively impact productivity. Subcontractors should also be aware of the following factors that impact worker productivity:
- COVID-19 — More and more construction companies realize the importance of cloud-based platforms. Cloud-based construction project management software delivers a useful social distancing tool by enabling teams to move from paper-based workflows to a digital workflow, eliminating the need for paper and minimizing face-to-face interaction. Through mobile apps, information can easily be collected from the field for the office to review whenever they are in the office or they are home.
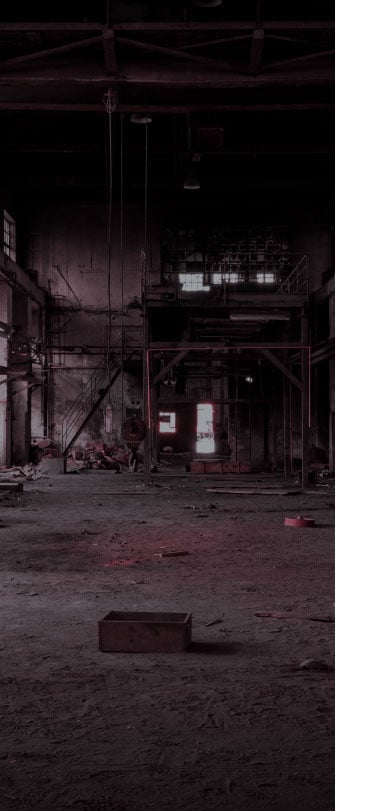
- Overtime — When a subcontractor is forced to schedule extended work days that exceed the standard 40-hour week, worker output may decrease because of physical and mental fatigue. This effect combined with the increased cost of overtime pay can result in significantly decreased cost efficiency for the subcontractor. The productivity loss could be even larger if the workers are assigned overtime during holidays.
- Joint Occupancy — When the construction schedule requires different trades or crafts to operate in the same work area on the job site, it can result in congestion and inefficiency as trade crews counter-productively block each other from operating at their most efficient productivity levels. Having too many workers in the same area can also expose workers to additional safety hazards.
- Start/Stop — Frequent work stoppages prevent workers from building momentum and getting into a rhythm. This includes scheduling or reassigning work during holidays.
- Logistics — A major cause of productivity loss on construction job sites is poor logistics and materials handling. Sometimes, the project owner wants to provide the materials for the work and subcontractors may be stuck waiting for a late delivery. Insufficient supplier controls or uncoordinated procurement practices can also cause shipping delays that leave workers sitting on their hands at the job site.
- Errors and Omissions — A project schedule that is incorrect or incomplete can have a disastrous effect on labor productivity. Comprehensive scheduling helps to ensure that construction tasks are accomplished in the right order and they help the subcontractor avoid inefficiencies and rework that arise from poor communication and inaccurate documentation.
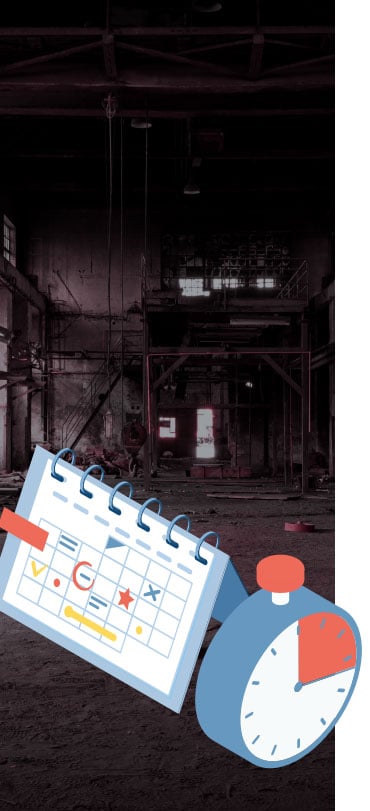
Poor Contingency Planning and Risk Management
Data from the United States Census Bureau indicates that new construction companies have the lowest percentage survival rate of new companies in all industries, with just 36.4% of construction companies staying in business for five years. Construction is inherently one of the most risk-laden industries in which to do business, yet many subcontractors are guilty of either implementing an arbitrary risk management process or overlooking risk management altogether. With knowledge of the high failure rates within the construction industry, poor contingency planning and risk management represent the height of foolishness for subcontracting organizations that hope to stay in business.
Subcontractors need to be aware of what factors elevate the risk in the construction business. These include:
- Frequent change orders that lead to cost and schedule overruns
- Disputes and litigations with project owners
- Completion for work which drives down prices
- Low-profit margins on projects with large turnover and profit risks
- The pressure to save time and money; hit financial targets by completing work quickly and cheaply
- Pressure to comply with health and safety regulations
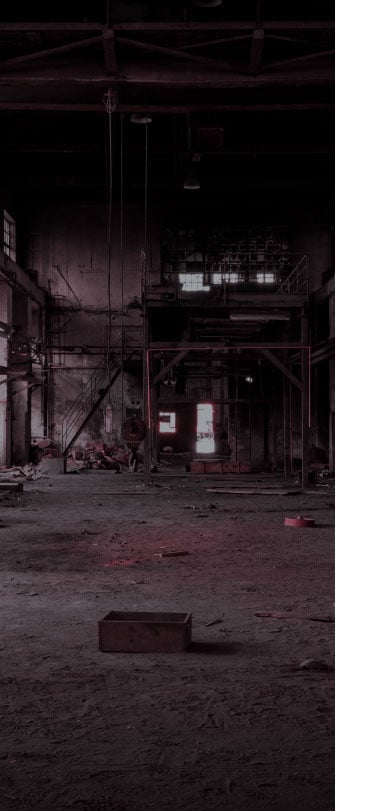
The best way to deal with risk on construction projects is not always to add a 10% risk management contingency to the project estimate, as has become common practice for subcontractors, but to preform a detailed and comprehensive risk assessment that seeks to identify and address potential weaknesses and source of risk before they start costing the organization time and money. Subcontractors can use the following model for conducting their project risk assessments:
- Identify potential hazards — Project managers need to identify all types of hazards that could affect project success and document them in a comprehensive list. Technical and logistical hazards can be controlled directly through adequate planning, while things like environmental and socio-political risks may be out-of-hand. Client risk can be addressed through effective relationship management with project stakeholders.
- Identify the result or who would be harmed — For each identified risk, the project manager should assess how the risk or hazard would impact the project.
- Quantify the risk — Use a numerical system to designate a relative risk score to each item, based on its likelihood and magnitude of the impact.
- Determine what control measures are needed — For each identified risk, the project manager and collaborators should work together to design and implement control measures that will reduce the overall risk to a more acceptable level.
- Re-qualify the risk — Once control measures have been agreed, we can re-evaluate the new overall project risk and determine whether it is beneficial for the company to work on the project.
- Document your analysis — Some contractors use a risk assessment form to document each identified hazard, how the impact was quantified and what measures are being taken to mitigate the risk. Sharing the risk management plan with project stakeholders and workers on the job site can increase awareness of known risks and help workers avoid them.
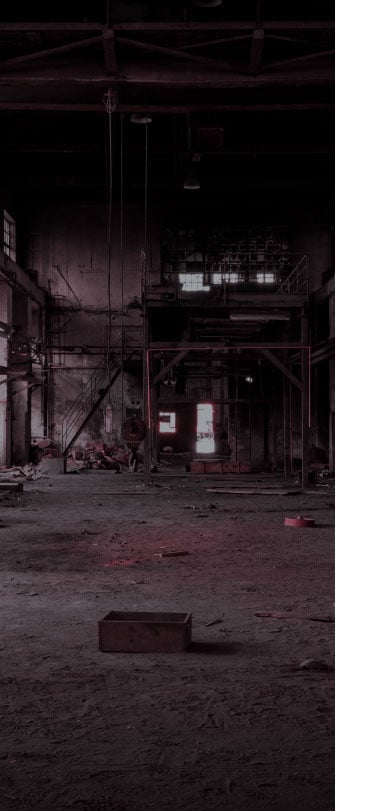
- Create contingency plans — Project managers need to look at the biggest and scariest risks and make clear, actionable contingency plans for how they will respond. A well-developed contingency plan implemented in a timely fashion is an excellent means of avoiding project delays and staying on-budget.
- Continuously monitor and review risks — Project managers must monitor job site operations and make changes to the risk assessment to reflect the changing risk profile of the job.
Timely, accurate, bi-directional flow of information between the office and the job site is necessary to ensure adequate risk monitoring on projects. eSUB’s construction project management software facilitates electronic daily reports that keep project managers and other stakeholders aware of what is happening at the job site, enabling fast deployment of contingency plans when a risk materializes.
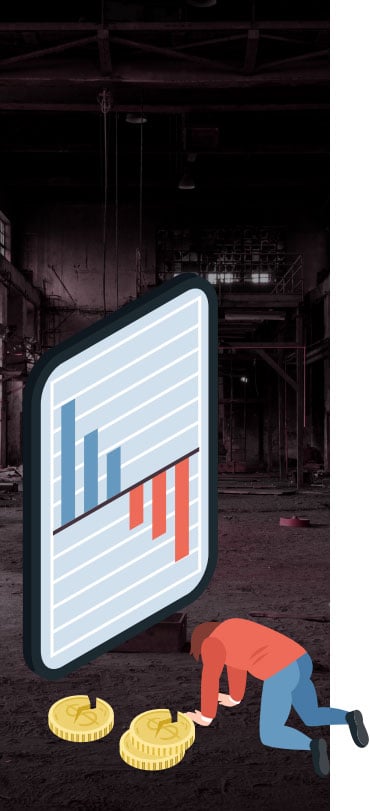
Incompetent Financial Management
With all the risks that constructions and subcontracting firms face just to do business in the industry, effective financial management is imperative to ensure that they earn a profit and stay in business. A report released by the Surety Information Office identified accounting issues as a top-five reason that contracting businesses failed during a two-year period, with 29% of the analyzed cases showing evidence of poor financial management as a root cause of failure. The report identifies four major issues that were present in these firms:
- Inadequate cost and project management systems
- Inadequate cost and project management systems
- Lack of adequate insurance
- Improper accounting practicess
The report also identifies “unrealistic growth” as a factor in 37% of failure cases, which begins to tell a scary story about how these contractors write their own death warrants in the industry. Many contractors simply take on too much risk, both on individual projects, and as a company overall. They set unrealistic growth targets with minimal room for error and borrowed up to the limits of their bank lines of credit to fund the upcoming projects.
Improper accounting practices means that the subcontractor is often not aware of its poor financial position until it is too late. Cash flow projections may be inaccurate or not done at all, and once the cash runs out (it is all tied up in projects), the subcontractor has no flexibility left for unforeseen expenses. Bills get paid late and vendors start demanding cash-on-delivery for material shipments. Profits start to dwindle, as the cost of deal with poor financial management starts eating into projected returns from projects, revenue and margins decrease and eventually, the firm declares bankruptcy.
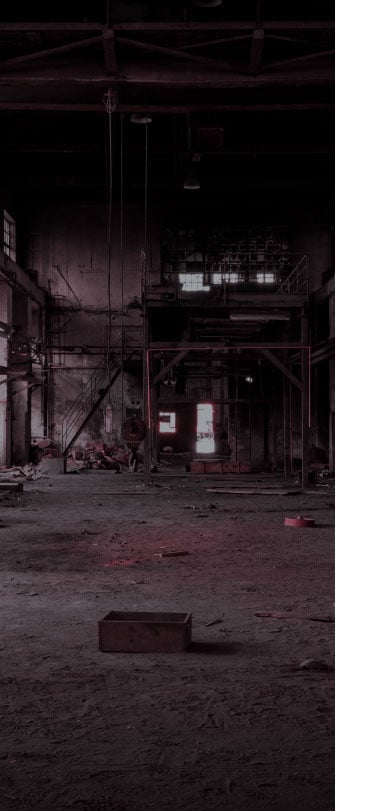
Subcontractors need to focus on sound financial principles, beginning with the CFO whose role requires accurate financial reporting, effective management of cash flow and liquidity, compliance with state and federal regulations, ensuring job profitability and oversight of all accounting operations. Productivity tracking and the utilization of job costing data in the bidding process are necessary for effective financial management, but subcontractors should also:
Negotiate Contracts to Maintain Cash Flow
Subcontracting organizations need to seek out project and payment terms that allow them to maintain healthy cash flow and liquidity throughout the project life cycle. Progress payments and milestones should be negotiated to ensure that the subcontractor is paid on a schedule that facilitates this. Subcontractors should submit payment requests using the AIA Application and Certificate for Payment form G702.
Establish Policies for Securing Payments
Subcontractors need to hold project owners accountable for paying on schedule, especially by establishing policies that incentivize early or on-time payments for the project owner. Offering a small discount for on-time payment while charging interest on late progress payments can help maintain cash flow while helping to guarantee that the project will comply with the payment schedule.
Integrate Accounting and Project Management
Subcontractors that successfully integrate their project management and accounting practices can leverage automated features that increase the accuracy of financial data and promote consistency between systems. eSUB’s construction management software platform offers integration with many different accounting software systems.
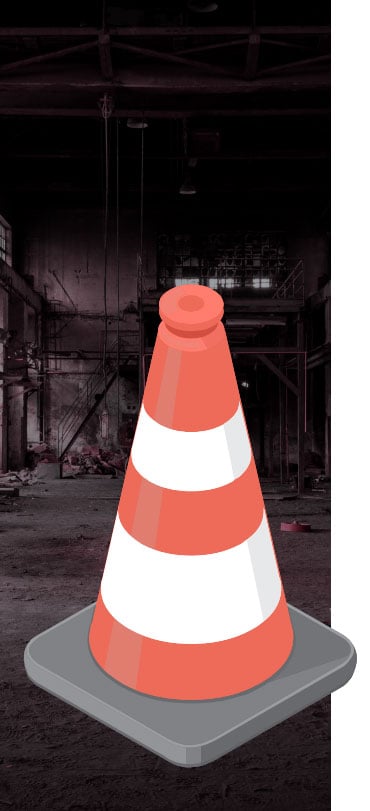
Lack of Attention to Safety Standards
Hazardous working environments are a normal part of the construction industry, where workers are exposed to toxic chemicals, heights, and other potential hazards each day. Approximately 20% of all workplace deaths in the United States in 2013 happened in the construction industry, with the leading causes including trips and falls, workers being struck by objects, electrocution, or workers caught in or between heavy objects.
Subcontractors and other employers in the construction industry need to take the lead when it comes to providing a safe work environment for their workers – or face the wrath of regulators. In the United States, the Occupational Safety and Health Administration (OSHA) conducts job site inspections to ensure that construction companies are operating in compliance with workplace health and safety requirements. Here’s what can happen when employers in construction ignore safety standards:
- Samsung Guam, Inc – In 1995, inspectors from the Labor Department visited a job site at Guam’s International Airport operated by Samsung Guam Inc. The firm was found guilty of 118 willful workplace safety violations, including instances of unsafe scaffolding that led to a high number of falls that resulted in at least one death. As a result, the firm was fined $8,260,000.
- G Industries, Inc. – In 2010, construction subcontractors at a power plant in Connecticut caused an explosion that injured over 50 people when they shot flammable gas down a pipe while attempting to clear the pipe of debris. The U.S. Labor Department indicated the company had ignored industry procedures, tossed aside their own safety guidelines and abandoned common sense, and they were ultimately fined $8,347,000.
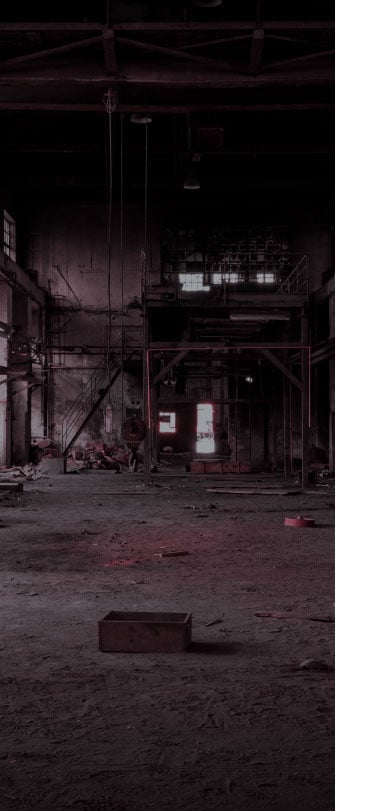
Great White Construction – In 2017, the inspection of two job sites operated by Great White Construction, a Jacksonville, Florida-based subcontractor, led to massive fines in connection with inadequate fall protection, eye hazards and other sub-standard safety measures. The company was identified as a severe violator, having received 22 similar citations dating back to 2012, and was thus subject to more severe financial penalties that reflect its ongoing non-compliance. The firm was fined a total of $1,523,710.
A lack of attention to safety standards can damage a subcontracting company beyond repair. In addition to massive fines from regulators, civil action from an injured person or their family can also prove expensive. Team morale and worker productivity also decline after workplace injuries. Contractors in the United States can now be sanctioned by OSHA when their subcontractors fail to provide a safe work environment, so subcontractors are risking further litigation and damage to their relationships in the industry when they receive citations. There are also project delays, reputation damage, and the possibility that perceived unsafe conditions will trigger staff turnover, leading to more project delays.
Subcontracting firms need to implement effective safety measures to protect workers as part of an overall risk management and project success strategy.
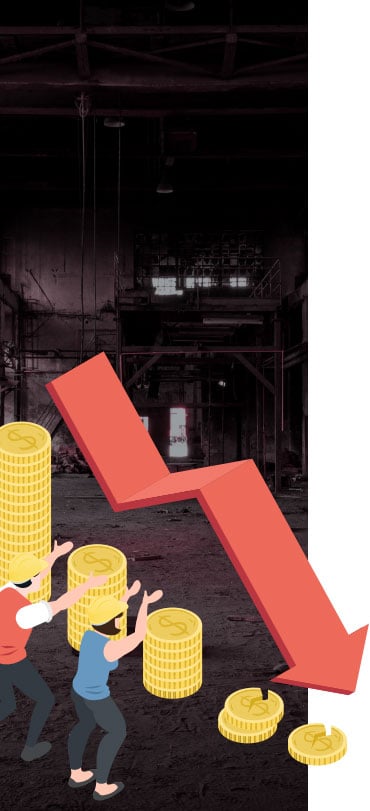
Inaccurate Job Costing
and Project Estimates
Poor job costing practices is a leading cause of business failure in the construction and subcontracting industries. Unlike other industries where revenue is generated by selling a product or delivering a service, the construction industry is almost entirely project-based. This makes it difficult for subcontractors to accurately determine project costs, as every new project has unique characteristics that differentiate it from work that subcontractors have done in the past. Subcontractors need to be aware of the most common types of estimating errors that result in inaccurate cost models, unrealistic estimates and profit loss, management starts eating into projected returns from projects, revenue and margins decrease and eventually, the firm declares bankruptcy.
Omissions – When subcontractors fail to include actual sources of the project cost in the estimate, it spells major trouble. Items that are left out of the overall project plans and specifications will not be included in the estimate and bid, but the project owner will expect to see those items with the finished product. Omissions can include direct construction costs such as materials on labor or indirect costs like fees or material transportation.
Incorrect Assumptions – When subcontractors base their bid on a set of assumptions that turns out to be incorrect, it can lead to poor job costing estimates. For example, if the subcontractor optimistically assumes that all resources will perform at 100% capacity, when it is more probably that resources will perform at 80% capacity, an incorrect cost estimate is likely to follow. A comprehensive risk assessment can help identify and address potentially harmful assumptions in the project plan.
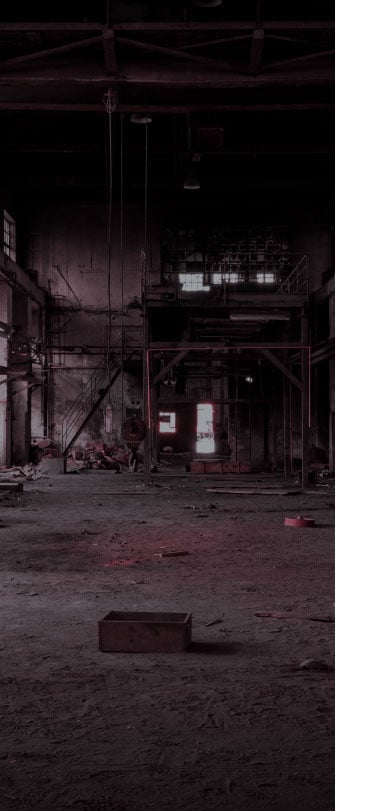
Inadequate Allowances – In their project estimates, subcontractors give allowances for materials, labor, transport and other broad expense categories. Sometimes, subcontractors face pressure to low-ball these estimates to improve their chances of succeeding with a bid, only for it to back-fire when cost overruns happen.
Price Changes – Changes in material costs, labor costs, or even the introduction of new tariffs in the marketplace can throw off job cost estimates.
Lack of Experience – When a subcontractor uses new materials or implements new working techniques on a project, there is typically a learning curve associated with the new implementation. Work may take longer than expected, and labor productivity may suffer as workers get accustomed to the new materials and processes.
eSUB’s construction project management software platform makes it easy for subcontractors to store, manage and access all their current and historical job-costing data. Subcontractors can deploy eSUB in the cloud, ensuring that job costing information can be retrieved from the office, the job site, and just about anywhere else that it could be needed. With eSUB, job costs are captured and is easily referenced to extract information for future bidding and project estimates.
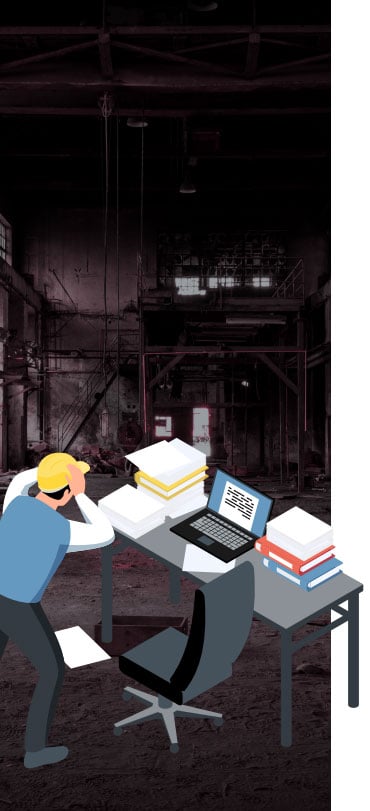
Poor Project Visibility
The Seventh scary construction project management mistake that we have identified is poor project visibility. Project visibility refers to the ability of project managers in the back office, along with other stakeholders, to access real-time or near-real-time updates on work progress and obstacles on the job site. Project managers rely on daily progress reports from the job site for updates into how work is progressing, but when faced with time constraints and budget pressure, on-site foremen may neglect to submit reports on time, disrupting communication with the back office and adding significant risk to the project.
Daily reports provide the back office with a comprehensive overview of how work is progressing on the job site. Each daily report includes the date and name of the person who filed the report, a description of weather conditions on the job site, details about physical site conditions, names of anyone who visited the job site that day, and information on available resources on the job site. Foremen should also describe what work has been completed, any current or anticipated future delays, what materials were received at the job site and any safety incidents or information that needs to be reported.
Real-time labor tracking with digital time sheets is one of the best ways that subcontractors can leverage technology to improve visibility of the job site and enhance labor productivity tracking to support more productive workers. Digital time sheets replace the paper time sheets that workers are accustomed to submitting at the end of each week – instead, the foreman captures hours worked, individual employees clock in and clock out on their mobile device, or a digital time clock kiosk is set up. Digital time sheets allow project managers to accurately monitor labor hours and cost throughout a project and create real-time visibility of labor productivity.
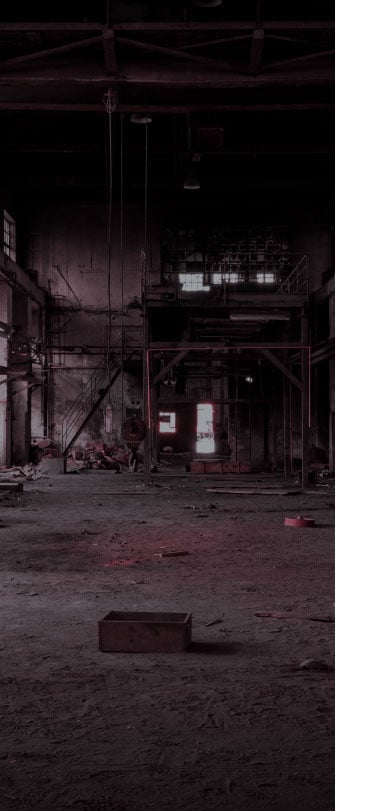
Digital daily reports can be submitted from the job site to the back office, eliminating the need for a construction foreman to fill out a paper report and deliver it to the project manager at the end of each day. Digital reports are more convenient, easier to complete and trace, and facilitate better accountability for submitting reports each day as required. Digital progress reports can be stored in a central repository where they can be accessed in real-time by all project stakeholders and kept secure in case they are required as evidence in future litigation.
Streamlined file sharing between the back office and the job site is essential for promoting project visibility. When a delay arises or a risk materializes, the ability to quickly share information, documents, drawings and images to address the issue in a fast and effective way is critical to limiting the potential impact of an adverse event.
Improving project visibility through technology should be a priority for subcontractors, as a lack of communication and coordination between the office and the field delays the response to any problem on the job site that threatens project success. With eSUB’s construction management software, subcontractors can implement real-time field data collection and labor tracking while enabling streamlined file-sharing through a secure, cloudbased application.
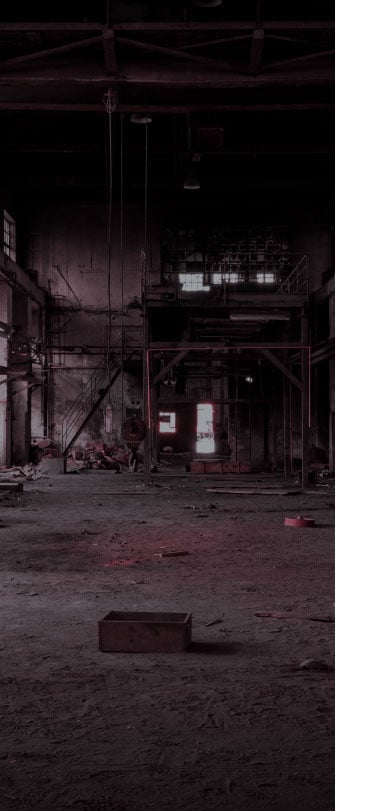
Summary
To succeed in construction over the next decade, subcontractors need to implement new policies and procedures to address the seven deadly sins of construction project management and weed them out of their organizations once and for all. With better document controls, labor productivity tracking, financial and risk management, project visibility, attention to safety and more accurate job costing, subcontractors can overcome the inherently risky business of construction and succeed in 2023 and beyond.
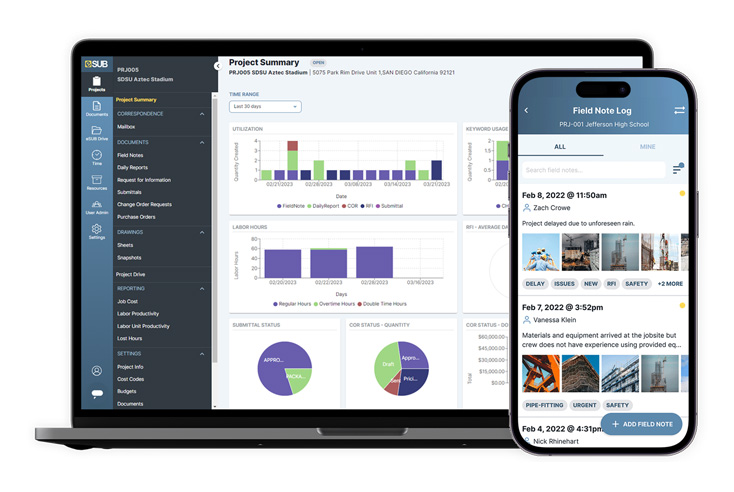